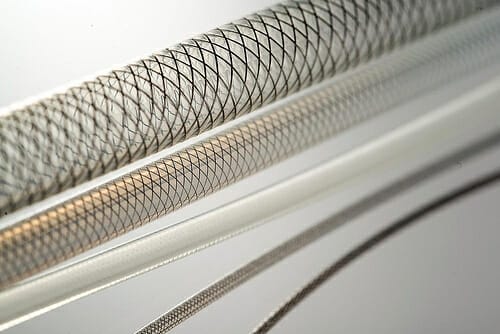
What is braided catheter tubing?
Braided tubing is an extrusion which encapsulates a metal or fiber braided configuration between two polymer layers.
Adding braided reinforcement to the thin wall of plastic tubing can improve burst pressure resistance, column strength and torque transmission. Braid angle and percent coverage are important, as well as size, shape and strength of the reinforcing material.
What options does Putnam Plastics have for braided medical tubing?
Depending on the amount of flexibility and torque required for your medical device application, Putnam can modify the braid angle to fit your needs.
- A smaller braid angle results in a tube with more column strength, higher torque and less stretchability. A larger braid angle results in greater kink-resistance but lower torque transmission.
- Flat wires provide a lower tubing profile and rounded wires offer higher tensile strength.
- Putnam Plastics can produce braided shafts with teflon or other lubricious liners. The shaft can be made in a single or multi-lumen structure. The components can also be produced with variable durometer polymers throughout the shaft.
Why would you choose a braided tube extrusion?
If you want improved torque properties such as torque transmission that translate into added pushability and steerability for medical catheters, then consider a braided shaft. A braided extrusion also provides additional column strength, burst pressure resistance, and an increased kink radius.
What materials is braiding typically comprised of and why?
- Putnam offers stainless steel, nitinol, Kevlar, Vectran, and polymer fibers to name a few. These are incorporated into extruded tubing ranging from 0.010 to 0.450 inches (0.025 to 1.143 cm) in diameter.
- The specific braid type will depend on your performance requirements.
What kinds of materials can be used for the inner lining of a braided-reinforced catheter shaft?
Inner liners can be produced from virtually any thermoplastic. Commonly the inner and outer materials are the same, but more lubricious liners such as teflon, HDPE and doped pi-conjugated polymers are also available.
What kind of sleeving or outer lining typically cover braided medical tubing?
The outer layers are commonly produced with a thermoplastic material (such as pebax or nylon.) Variable durometer polymers can be used on the distal and proximal sections—to create a soft tip while maintaining good torque and pushability on the proximal end.
What range of picks per inch (PPI) does Putnam offer?
Reinforcing braids are available in complete coverage up to approximately 1 pick/inch (0.39 wraps/cm).
What other technologies can be combined with reinforced braiding?
Our variable braiding technology can translate into a higher angle braid at the distal end for more flexibility, and lower angle braid at the proximal end for more column strength and pushability. Other options include:
- Polyimide liners
- Teflon liners
- Multi lumen shafts
- Variable durometer shafts
- Combination of thermoplastic and thermoset shafts
What medical devices, body parts or procedures are these commonly used in?
Braided tubing is used in a variety of medical applications including cardiovascular and neurovascular surgeries, and endoscopic procedures such as those through the gastrointestinal system. Other common uses for this extrusion:
- Electrophysiology (EP) catheters for diagnostic purposes
- Ablation catheters
What ISO certifications is Putnam equipped to comply with?
Putnam Plastic’s premier custom tubing manufacturing facility is ISO 13485:2016 certified. Our designated clean room space meets the demand for greater regulatory controls for thermoplastic extrusion and finishing components of medical devices.
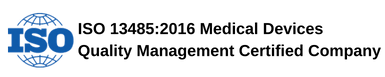
Why is Putnam Plastics the best choice for this product?
Putnam’s braiding machines can change braiding rates during operation to create tubing with different braid flexibility between the proximal and distal sections of a shaft without the expense or risk of a molded joint. Higher percent coverage can also add to kink resistance, torque transmission, and pressure resistance.
Putnam Plastics is a high-tech extrusion leader, our top-notch engineers have been solving medical tubing challenges for over 40 years. Speak with a Putnam engineer or sales representative about your braided medical tubing needs today.