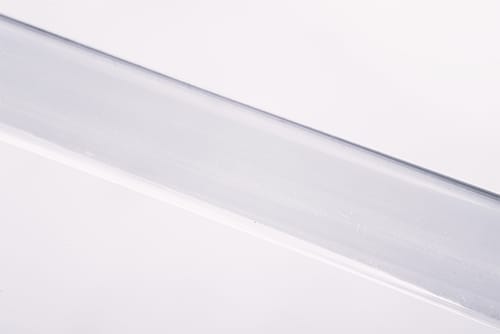
What is FEP heat shrink tubing?
FEP heat shrink tubing is heat shrink made from FEP (fluorinated ethylene propylene) and is used for reflow of material in a catheter assembly process. Compared to other heat shrink tubing such as PTFE, FEP heat shrink has a lower melt temperature. It is typically a processing aid used in the formation of a catheter assembly.
What size FEP heat shrink tubing is available?
Putnam’s FEP heat shrink wall thicknesses range as low as 0.004” in diameter up to 0.020”, providing flexibility to meet specific application requirements. Additionally, Putnam’s heat shrink offers expanded inner diameters up to 0.375” and an expansion rate of up to 1.7x the original size. Custom sizes and lineal shrinkage are available as well.
Putnam Plastics’ FEP Heat Shrink Tubing Standard Sizes
Expanded ID (in) | Recovered ID (in) | Wall (in) |
---|---|---|
0.31 | 0.249 | 0.012 |
0.27 | 0.18 | 0.012 |
0.25 | 0.15 | 0.012 |
0.213 | 0.142 | 0.012 |
0.315 | 0.2 | 0.012 |
0.176 | 0.11 | 0.01 |
0.213 | 0.138 | 0.006 |
0.213 | 0.138 | 0.008 |
9.213 | 0.138 | 0.009 |
9.213 | 0.138 | 0.01 |
0.375 | 0.225 | 0.012 |
0.135 | 0.085 | 0.01 |
0.32 | 0.2 | 0.01 |
0.24 | 0.15 | 0.01 |
0.3 | 0.187 | 0.01 |
0.093 | 0.056 | 0.01 |
0.125 | 0.075 | 0.01 |
0.188 | 0.115 | 0.01 |
0.25 | 0.15 | 0.01 |
0.182 | 0.147 | 0.006 |
0.18 | 0.143 | 0.01 |
0.098 | 0.07 | 0.009 |
0.052 | 0.032 | 0.009 |
0.15 | 0.094 | 0.01 |
0.06 | 0.038 | 0.008 |
0.112 | 0.077 | 0.008 |
Why choose Putnam’s FEP heat shrink tubing over competitors’?
Unlike other technologies in the industry, Putnam’s FEP heat shrink tubing is manufactured without any processing aids such as silicone oil, eliminating potential bonding and contamination issues commonly associated with traditional heat shrink materials. Featuring less than 5% lineal shrinkage, Putnam’s FEP shrink tubing may also provide increased tensile values and higher overall yield rates for certain bonded catheter assemblies. Recent investment into increased capacity at Putnam Plastics has allowed quick turnaround time for FEP heat shrink tubing that can be as quick as 4 weeks.
What is FEP heat shrink typically used for in medical devices?
FEP heat shrink is possibly the most used processing aid for catheter assembly in the medical device manufacturing industry.
What ISO certifications is Putnam Plastics equipped to comply with?
Putnam’s state-of-the-art plastics extrusion manufacturing facility is ISO 13485:2016 certified.
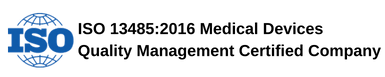
Why is Putnam Plastics the best choice for PTFE coated mandrels & wire?
Putnam has been coating wires and mandrels for nearly two decades. Our engineers are available to assist in material selection and optimization, ensuring that the polymer coating that is ultimately selected is best suited to meet specific product performance requirements. We offer in-house testing for all adhesion and coating processes. By providing both manufacturing and testing under one roof, customers benefit from a reduction in lead time and access to product design that is customer specific. Samples are also available in formats that will allow customers to evaluate bond strength, frictional properties and durability.