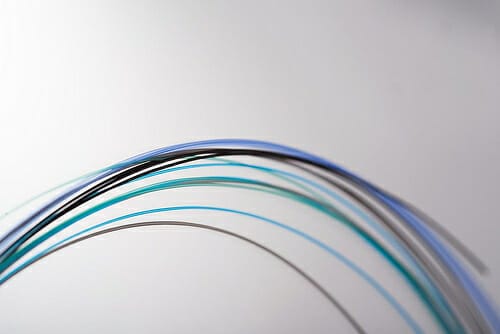
What is a tri-layer extrusion?
A tri-layer extrusion is a single lumen tube comprised of three discrete layers.
What materials are used in a custom multi-layer extrusion?
Putnam Plastics has the ability to design and build the widest range of two and three layer material combinations. These combinations can include, but are not limited to
- Pebax
- Nylon
- Polyurethane
- Polyethylene
- Polyester
- Teflon
- Polyimide
- PEEK
What options should you keep in mind when procuring multi-layered medical tubing?
Tri-layer tubing is often recommended when a single material extrusion will not meet your performance requirements. A tri-layer structure allows the extrusion to have unique characteristics throughout the tube.
- Lubricious ID: Tri-layer designs can incorporate specific materials on the inner diameter to improve ID frictional properties.
- Physical Properties: Tri-layer tubing can be designed with one of the layers ideally suited to increase burst strength, decrease elongation or improve tensile strength.
- Bondability: Tri-layer tubing offers the option of an outer material layer that allows for proper adhesion of ink, or bonding to other thermoplastics components.
- Delamination: Tri-layer tubing provides two non-compatible materials the ability to bond together.
- Encapsulation: Tri-layer tubing allows a non-medical material/ingredient to be encapsulated between two medical-grade layers.
What other tri-layer extrusion options does Putnam Plastics have?
Putnam Plastics can customize the level of radiopacity, chemical resistance and light permeability, and incorporate active materials that are water dissolvable or bioresorbable.
Can Putnam Plastics bond two chemically dissimilar materials using a tie or bonding layer?
Through our tri-layer technology, Putnam Plastics has the ability to bond chemically dissimilar materials. The most commonly requested combination is a Pebax outer covering with a Polyethylene inner layer.
What other Putnam technologies can be used with a tri-layer extrusion?
Putnam Plastics tri-layer tubing can be used as a stand-alone technology or incorporated into a more complex extrusion design, such as our new Super-Tri™ technology.
If you require a cost-effect continuous manufacturing approach for a guide catheter, see our Tri-TIE™ page.
Can more than 3 layers be extruded together?
Putnam Plastics has the ability to extrude additional layers, and has produced a 4-layer extrusion.
Why would you choose this type of extrusion technology over others?
Many medical device requirements cannot be met with a single raw material. With multiple material design, engineers can optimize the shaft performance—so your medical device operates exactly as you specify.
What medical devices or procedures is this commonly used in?
A variety of medical devices assemblies can benefit from tri-layer extrusions:
- Tri-layer extruded tubes are used in catheter systems that navigate deep into the vascular system by following a preplaced guide wire. Tri-layer extrusions are also used as working channels within a catheter assembly to allow for insertion of a tool or implanted through the lumen to the therapeutic site.
- Percutaneous transluminal coronary angioplasty requires a lubricious inner lining. A tri-layer extrusion with a stiffer middle layer provides better burst resistance without increasing wall thickness.
- Multi-layer tubing can combine low-density polyethylene (excellent for transporting an infusion solution) on the inner layer with PVC on the outer sheath to give kink resistance.
- Other medical devices and procedures that can benefit from tri-layer extrusion include implantable central venous catheter, coronary implant delivery system, dialysis and stenting.
What ISO certifications does Putnam Plastics have?
Our premier medical manufacturing facility is ISO 13485:2016 certified. Our ISO Class 8 clean room meets the demand for greater regulatory controls for extrusion and finishing components.
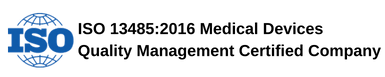
Why is Putnam the best choice for this multi-layer extrusions?
Putnam Plastics has been the pioneer in multiple layer extrusion technology for over 40 years. Partnering with Putnam means working with a premier plastics science innovator.
If you are looking for expert custom designs, rapid turnaround prototypes and quality-controlled volume manufacturing, you’ve come to the right place. Contact us to speak with a knowledgeable representative today about your custom tubing needs.