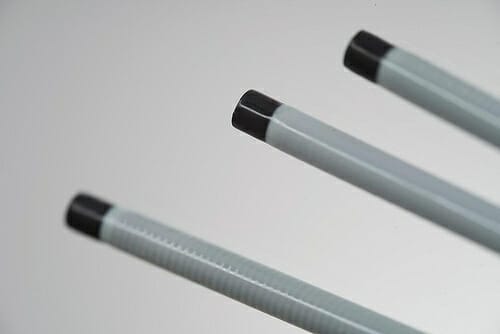
Why would you choose medical plastic laser welding?
Laser welding is a highly reliable and repeatable thermal bonding technology for joining medical catheter components, such as soft tips to more rigid catheter shafts.
Laser thermal bonding differs from traditional thermal bonding in that heat is generated through material absorption of laser light, which results in a more efficient application of heat. This makes it possible to create very small bonds between medical catheter device components without melting the surrounding surfaces.
What are the exceptional properties of laser welded medical plastics?
Our lasers produce a wavelength with similar resonance frequency to the polymers commonly used in medical catheters, which allows it to be absorbed by opaque and transparent components. It also provides for outstanding bond strength and smooth joint surfaces between mating components.
What are the advantages of laser welded catheter components?
- Smoother joints
- Ability to create a hermetic seal
- High joint strength for improved patient safety and reliability
- Stronger bond than RF bonding
Which materials are typically laser welded for medical catheters?
The application of laser bonding in medical catheters is dependent upon the materials of construction. Polymers commonly used for catheter manufacturing, such as Pebax, nylons and high density polyethylene (HDPE), are good candidates for laser bonding.
What other Putnam technologies can be combined with laser welded catheter components?
Our 2-axis bonding lasers have been modified to fuse soft atraumatic tips onto less flexible catheter shafts that use our braid or coil reinforced technology for increased strength, and short fuse downs of components.
What medical devices are laser welded components commonly used in?
A variety of medical catheters require soft tips and rigid shafts and can benefit from medical plastic welding. A few examples of this include:
- Guide catheters
- Micro catheters
- Neurological catheters
What ISO certification does Putnam Plastics have?
Putnam’s leading-edge medical manufacturing facility is ISO 13485:20016 certified. Our dedicated ISO compliant cleanroom manufacturing space meets the growing demand of regulatory guidelines.
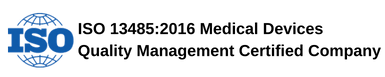
Why is Putnam the best choice for plastic laser-welded catheter components?
To incorporate a laser-welded bond, the welding step must be considered during the design phase. Putnam’s in-house design and manufacturing departments means our engineers and laser technicians can work together to integrate design and implementation—and can smoothly make modifications as needed.
Putnam has the ability to laser bond and ablate to create custom catheters.
We house diverse operations specifically designed for catheter components—such as printing, welding and overmolding—under one roof to give you the best speed to market for your custom tubing needs.